Using Innovative Technology to Repair Pipelines from the Inside
SBIR awardee QuakeWrap develops no-dig pipeline spot repair using material and automation technology
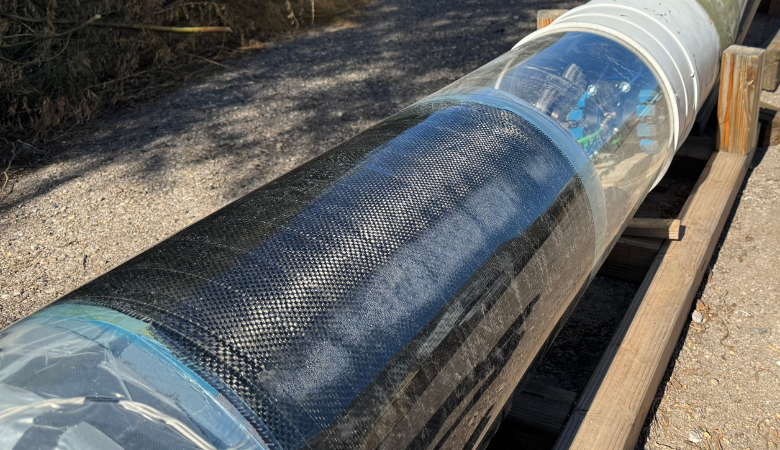
THE CHALLENGE
Funding Agency: PHMSA
Small business: QuakeWrap: https://quakewrap.com/
Project: No-Dig Point Repair Technology for Steel O&G Pipelines
Principal Investigator: Dr. Mo Ehsani
Location: Tucson, Arizona
Pipeline damage can be very dangerous, causing significant harm to communities when an incident occurs. The Pacific Gas & Electric Pipeline Rupture in San Bruno, CA devastated the community and resulted in the death of 8 people, 51 hospitalizations, and the destruction of 38 homes. For every large-scale tragedy like this one, there are many more pipeline leaks and punctures every year, which put lives at risk and cause serious environmental damage. Between 2019 and 2023, nearly 9.7 billion cubic feet of natural gas was released into the atmosphere from pipeline leaks, according to a Reuters analysis of PHMSA data. These human and environmental harms illustrate the pressing need for innovation in pipeline design and maintenance to improve safety and prevent similar incidents.
THE TECHNOLOGY
Pipeline operators conduct thousands of repairs each year on pipeline damage, typically requiring costly and disruptive excavation of the pipeline to repair the damage from the outside. Particularly problematic are repairs on hard-to-reach areas such as river and highway crossings.
QuakeWrap, a small business focusing on infrastructure repairs, developed a technology for no-dig point repairs of pipelines through DOT’s Small Business Innovation Research (SBIR) program’s Phase I and Phase II awards funded by the Pipeline and Hazardous Materials Safety Administration. (PHMSA). “Our solution can best be described as an ‘industrial stent,’” says QuakeWrap President and CEO, Mo Ehsani. QuakeWrap uses “SuperLaminat™," a technology consisting of sheets of a strong and lightweight carbon fiber fabrics soaked in epoxy resin, to repair pipe leak points from the inside. Sheets of SuperLaminate™ are wrapped around a packer, which is then attached to an Automated Guide Vehicle (AGV) on a tether. The AGV and packer are sent into the pipeline from a launch pad, and travel through the inside of the pipe to the point of repair. The packer then inflates and presses the SuperLaminate™ against the sides of the pipe. Once in place, a heating mechanism is activated to cure the laminate. When the curing is complete, the packer and AGV are extracted from the pipe, and the SuperLaminate™ repair sleeve remains in place inside the pipe, much like a medical stent.
QuakeWrap’s repair solution can be deployed from existing tool launchers and travel through bends and slopes in the pipeline, so the technology eliminates the need to dig trenches for spot repairs. This makes it much less disruptive and destructive to surrounding communities and much less costly for pipeline operators to make this type of repair.
For oil and gas transmission pipelines, it is essential that the SuperLaminate™ repair material be able to withstand high pressure and resist chemical damage it will face transmitting these substances. Testing the SuperLaminate™ system for these properties critical for oil and gas transmission has been a focus of QuakeWrap’s SBIR research.
SBIR’S ROLE
QuakeWrap’s Ehsani shared that DOT SBIR funding has played an essential role in the development of their no-dig repair technology for repairing steel oil and gas pipelines. The SBIR award “has played a significant role by providing the financial means for a small company like us to develop this technology; without this support, we would not have pursued this endeavor,” said Ehsani. He also noted that participation in the DOT SBIR program helps give small companies like QuakeWrap more legitimacy as they introduce their novel technologies to established industries.
THE FUTURE
Corroding and leaking pipes are a major safety and environmental concern. Looking forward, QuakeWrap CEO Ehsani says the company intends to extend the reach of their tethered AGV deployment technology, which currently has a reach of 500 feet from the deployment site, in order to be able to reach a greater range of repair sites. Ehsani says the company is currently making minor improvements before commercializing the technology and has been contacted by a major pipeline owner to discuss potential sites where they could perform pilot field installations. The successful completion of these pilot projects should help introduce this technology into the broader industry.
Easier methods for repairing pipelines could have important safety and environmental benefits. In addition to preventing and mitigating dangerous leaks, Ehsani says this technology can help keep existing pipelines in service longer. “By repairing the existing network of pipelines, the service life of these facilities can be safely extended,” says Ehsani “This also helps eliminate the need for building new pipelines which is a growing environmental and political concern." He also notes that the problem of corroded pipes is an issue affecting pipelines around the globe, and if successful, QuakeWrap’s technology has the potential to be implemented internationally.