Cracked Up—Broken Rails Are Serious Business
Nearly all cracks in rails are hidden—so says Dr. David Jeong, senior mechanical engineer at Volpe, The National Transportation Systems Center. Jeong and his colleagues, in support of the Federal Railroad Administration (FRA), have been examining the mechanics of metal fatigue and crack growth in the country's network of rail steel. In 2012, the largest railroads in the United States operated trains on over 112,000 miles of track. Including short-line railroads, the total track miles of rail steel in the U.S. is closer to about 150,000 miles.
"A third of all track-caused rail accidents occur due to broken rails or joints," said Jeong. "The majority of broken rails are caused by a particular internal defect called the detail fracture. These cracks start out too small to detect, but they grow as trains run over the rail." Calculations performed by Jeong and his team show that some cracks can increase in size very rapidly.
Special crack-detection vehicles carry ultrasonic probes to look for these cracks. The probes find some cracks once they grow large enough to detect—then the railroad removes the rail from service. But unfortunately some cracks are not detected by the probes. "Cracks may have complex shapes due to their three-dimensional character," said Jeong. "The probe's ultrasonic signal might miss the crack, especially if the rail is heavily worn. Surface damage on the rail head can also interfere with the ultrasonic signal."
A technical challenge for the government and the industry is to find out why some cracks escape detection. With concurrence from FRA, Jeong and the Volpe team have collaborated with the National Transportation Safety Board in some of the Board's accident investigations involving broken rails.
One of these investigations involved a westbound Amtrak train, the California Zephyr, which derailed near Nodaway, Iowa, in March 2001. A broken rail was discovered at the point of derailment. Seventy-eight of the 241 passengers on the train were injured, including one fatal injury. "For the Nodaway crash, two defects were found in the wreckage," explained Jeong. "Our role was to back-calculate the size of defects at time of the last inspection. These back-calculations tell us the sizes of the defects that were missed by the crack-detection vehicle."
Understanding why certain cracks escape detection may lead to improved detection practices in the future.
One of the major accomplishments of the Volpe team is the development of an algorithm to schedule the frequency of rail tests to detect cracks. "The algorithm is referred to as a performance-based or risk-based method because it assumes a tolerable level of risk. In this context, risk is defined in terms of the number of broken rails over a given line segment between test rails." The algorithm is programmed using macros in an Excel spreadsheet that they have shared with railroads, some of which are already trying it out.
Extreme weather and climate are increasingly affecting our rail system as well. "In the aftermath of Hurricane Sandy, the tunnels under New York City were flooded with salt water. The salt water could lead to corrosion and a different kind of cracking that occurs in the base of the rail. The railroads operating in the tunnels will have to consider the long-term impact of the flooding on the rails," stated Jeong.
See video highlights of Dr. Jeong's talk: Transportation Trajectories with Dr. David Jeong.
Photo above: Dr. David Jeong (Volpe photo)
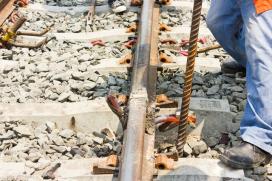